競馬学会は詐欺サイト?口コミや評判から徹底検証
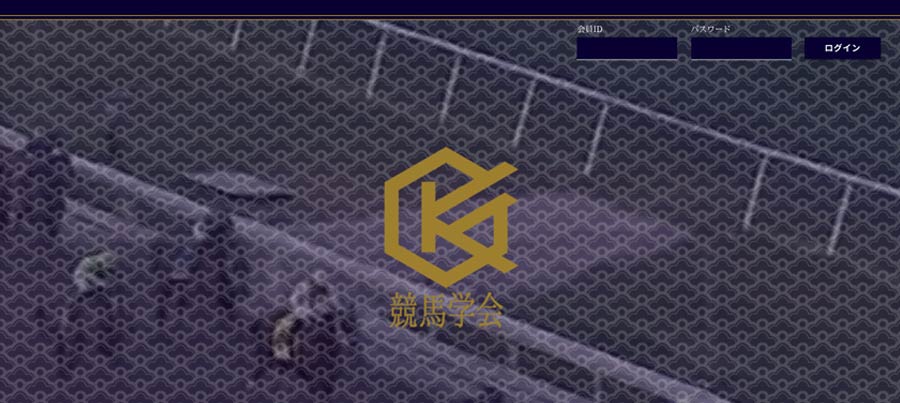
競馬は最大18頭でレースをする公営競技です。
競艇や競輪と比べると出走頭数が多いためその分買い目も増えます。
特にもっとも配当金が高くなる3連単をコンスタントに当てるのは、熟練者でも指南の業です。
あなたが、なかなか的中することができないのであれば、競馬予想サイトを利用してみてはどうでしょうか。
本記事では競馬予想サイトのひとつ、「競馬学会」について徹底検証していきます。
競馬学会とは?
トップページを見ていて、一番銘に泊まるのが「全額あんしん保障」という一文ではないでしょうか。
詳細を見ると、新規登録から90日間限定で、有料情報の情報料よりも配当金のほうが下回っていた場合は、情報料の全額をポイントで返還すると記載されています。
現金ではなく、ポイントで変換されるという点は勘違いしてはいけませんが、それでもトリガミになった場合は情報料を返還してもらえるというのはとても嬉しいサービスといえるでしょう。
また、競馬学会には複数の馬券師が在籍しており、それぞれ個別に有料情報を担当しています。
予想を出す手段は馬券師によって異なるので、プランの詳細を確認し、自分にあった馬券師を選ぶと良いでしょう。
「お客様の声」という項目があり、確認してみると、ほぼすべての口コミが稼げたというものばかりでしたが、全部が絶賛というわけではなく、トータルでは稼げているといったものも掲載されているので、捏造している雰囲気はあまり感じられませんでした。
競馬学会の運営会社の実態を調査
競馬学会の会社情報のうち、所在地を確認すると「東京都台東区竜泉3-8-4」となっています。
この場所を検索すると、ハンエイビルというオフィスビルが建っていました。
どの部屋を使っているのかまでは分からないですが、競馬学会はこのビルの1室を借りて運営しているのでしょう。
オフィスビルの1室を借りて運営している予想サイトは山のようにあるので、住所に関しては虚偽の記載をしているわけではなさそうです。
会社情報にはメールアドレスだけではなく、電話番号もしっかりと記載されていました。
電話番号が記載されているという事は予想に関して今すぐ質問したいといった場合でもしっかりと回答できる準備ができているという事なのでしょう。
少なくとも苦情が来るようなデタラメな予想は出していない事が分かります。
競馬学会の運営会社概要
競馬学会の運営会社の概要は、下記のようになっています。
個人で運用しているのではなく、法人で運営しているようです。
運営会社 | 株式会社フラクタリコ |
運営責任者 | 斎藤孝典 |
所在地 | 東京都台東区竜泉3-8-4 |
電話番号 | 03-6823-4578 |
メールアドレス | info@pxel.jp |
実際に競馬学会の無料予想&有料プランを買って検証
ここまで見る限り、競馬学会のサイト内容や会社の運営者情報には特に問題点などは見つかりませんでした。
しかし気になるのはやはり予想の的中精度です。
実際に競馬学会の無料予想、そして有料プランの予想をもとに、本当に的中するか検証してみました。
無料予想を検証
有料プランの検証の前に、まずは無料予想から検証していきます。
2月12日(土)の無料予想
対象のレースは2月12日(土)東京11Rデイリー杯クイーンカップです。
提供された予想は以下の通りでした。
2,4,7,9,13
(1点500円:計10点)
3連複のボックス買いの予想となっています。
前評判の高かった9番スターズオンアース、13番プレサージュリフト、2番ベルクレスタの3頭もしっかり買い目に含めており、比較的手堅い予想と言えるでしょう。
さぁ、最初の検証結果はどう出るでしょうか?
レースは中々の接戦となりましたが、1着に13番プレサージュリフト、2着に9番スターズオンアース、3着に2番ベルクレスタと人気馬が期待に応え見事3連複的中。
オッズは1番人気10.6倍で5,300円の的中とほぼ利益は出ませんでしたが、的中したのでまずは良しとしましょう。
有料予想を検証
無料予想ではオッズこそ低かったもののとりあえずは的中したということで、次に本命の有料予想の検証に移ります。
今回はTendence、Feeling Jockeyという2プランに参加してそれぞれ検証を行いました。
2月13日(日)の有料予想「Tendense」の検証
最初の検証はTendenseというプランで行います。
こちらは競馬学会の中でも高配当を幾度も叩き出しているプランとのことで、なんでも「予想師の勘を頼りに予想を提供するプラン」とのこと…。
説明文を見て少し購入迷いましたが、的中実績も数多く開示されており、今回は検証ということもあるので真虚を確かめるべく思い切って参加することにしました。
提供された予想は以下の通りでした。
1着:12
2着:1・8
3着:1・5・8・9・11・13
(1点500円:計10点)
3連単フォーメーション買いで1番人気のバトーデュシエルを軸に置いていますが、2着に13番人気のベンガンを入れているところに注目したいです。
果たしてこの選択が吉と出るか凶と出るか…。
レースの結果は…。
レースは1着に1番人気の12番バトーデュシエル、そしてなんと後方から脅威的な追い上げを見せた8番ベンガンが見事2着でゴール!
3着には5番ホウオウエンジェルが食い込みなんと3連単的中!
オッズは高め1837倍、払い戻し金は918,500円となりました…!
いやぁ…予想師の勘恐るべしと言ったところでしょうか。
2月13日(日)の有料予想「Feeling Jockey」の検証
本来なら先程の高配当で勝ち逃げするところですが、今回は検証ということでもう1レース勝負していきたいと思います。
次の検証は「Feeling Jockey」という騎手にスポットを当てているプランで、こちらも競馬学会の中では高配当が当たると評判の人気プランのようです。
提供された買い目は以下の通り。
1着:14
2着:3・4・5
3着:3・4・5・11
(1点600円:計9点)
前回同様こちらも3連単フォーメーション軸1頭という買い目で、競馬学会のプランは他の予想サイトと比較しても、買い目点数を絞ったピンポイントの予想という印象があります。
今回軸に置いた14番タイセイグラシアの騎手を務めるのは「古川奈穂」騎手です。
古川奈穂騎手はとてもルックスがよく可愛い女性騎手として有名ですが、その実力は確かなもので、今回のレースも期待したいところです。
果たして結果はどうなったでしょうか?
レースは残り400m付近から古川菜穂騎手が乗るタイセイグラシアが先頭に抜け出します。
そこから粘り強い走りで直線を駆け抜け、後続馬を押し切りそのまま1着で見事ゴールイン!
2着には4番メイショウミズモ、3着に11番ジュランドが入り見事3連単的中!
オッズはまたも高め1128.4倍の払戻金677,040円の高配当となりました…!
払い戻し金:1,600,840円
馬券代:15,400円
情報料:160,500円
利益:1,424,940円
今回の検証をまとめると上記のような結果となりました!
まさか3連続的中とは…!お見それしました…。
もちろん毎回このように上手くいく訳ではないですが、少なくとも今回の検証を見る限りは競馬学会の予想精度は十分信用に足りると思います!
競馬学会のメリット・デメリット
競馬は公営競技のなかでももっとも知名度が高く、愛好者が多いという事もあって予想サイトの数も数えきれないほどあります。
それぞれの予想サイトは競合他社に負けないよう独自の特徴を持っていますが、それがすべてのユーザーにとってメリットとなるわけではありません。
自分にとってメリットが大きい競馬予想サイトかどうかも、検証の際にはとても重要です。
競馬学会を利用することでどのようなメリット・デメリットがあるのか纏めました。
競馬学会のメリット
やはり90日間限定ではありますが、的中しない、あるいは的中しても情報料のほうが上回っている場合は情報料を全額ポイントで返還してもらえるというのは大きなメリットのひとつといえるでしょう。
有料情報はそれなりに高額なので、それなりにリスクが高いです。
高いリスクを冒してまったく当たりもしなかったら、金銭的にはもちろん精神的にも大きなダメージを負うことになります。
しかし、ポイントでの返還とはいえ、情報料が戻ってくるという安心感があれば、当たる当たらないを気にせず気軽に有料情報を利用することができます。
競馬学会のデメリット
競馬学会は予想を見る以外で会員登録をして利用できるものが一切ありません。
競馬予想サイトのなかには会員登録をすると、競馬に関しての情報やコラムなど、読み物を閲覧できるところがあります。
そういったところと比べると、コンテンツの内容はあっさりしているという印象を持ってしまうでしょう。
競馬学会は、予想を見たいときにだけアクセスする競馬予想サイトといえます。
また、有料情報の詳細は予想を出しているプランしか見る事ができません。
事前に情報を確認したいという人にとっては、不親切なサイトという評価になってしまうかもしれません。
事前に有料情報の詳細を見たいのであれば、中央競馬が開催されている土日にアクセスするのがおすすめです。
競馬学会有料情報の料金プラン一覧
現状確認できたプランのみを公開しているので、ここに紹介しているのが競馬学会の有料情報のすべてではない点はご了承ください。
プラン名 | 利用料金 |
スタンダード | 100ポイント(110ポイントで1万円) |
プレミアム | 300ポイント(340ポイントで3万円) |
GOLDSHIP | 38,000円 |
会心の一撃 | 50,000円 |
ACE | 62,900円 |
オイキリ・ジョー | 65,000円 |
Feeling Jocke | 14万円 |
Tendence | 17万円 |
花の慶次郎 | 21万円 |
VISION | 28万円 |
Potential lab. | 34万円 |
コルモゴロフ馬学 | 60万円 |
KINGS MAN | 62万円 |
プランの種類や特徴
それぞれのプランの詳細をチェックすると、どういった基準で予想をしているのかの説明を見る事ができます。
自分に合った有料情報を利用するのが競馬学会を最大限に活用するためのコツといえるでしょう。
ポイント情報
ポイント情報には、「スタンダード」と「プレミアム」の2種類があります。
スタンダードは100ポイント、プレミアムは300ポイントで利用可能です。
ポイント購入の有料情報は、「3連複」の予想となっています。
3連複はオッズは低いですが、的中率は3連単と比べるとかなり高いです。
手堅い予想を公開しているといえるでしょう。
募集人数限定の情報
各馬券師の予想は、主に中央競馬が開催される土日に公開している事が多いです。
各馬券師の予想は利用できる人数が限定されているので、有料情報を利用するつもりなのであれば、売り切れにならないよう早めにアクセスしておきましょう。
GOLDSHIP(ゴールドシップ)
馬券師はセリ市場で無数の馬を見てきた人物です。
その観察眼で、調子がよさそうな馬を見つけ、予想を出しています。
会心の一撃
会心の一撃は、競馬学会の登竜門と説明がなされてるプランで、費用対効果がかなり高い有料情報であるとアピールされています。
確かに情報料はまだお手頃な部類なので、無料情報である程度稼げたのであれば、挑戦してみる価値はあるでしょう。
ACE
ACEを担当する馬券師は元数学者という経歴の人物です。
競馬の予想をする際はさまざまなデータを分析することになります。
数学者ならではの分析力で独自の予想を導き出しています。
オイキリ・ジョー
追い切りは、レース前の情報としてとても重要ですが、オイキリ・ジョーはその追い切りで全てを見抜き、買い目を決めるというプランです。
Feeling Jocke
騎手にスポットを当てているプランで、担当者は騎手との強いつながりを持っています。
そのため、世間では語られることのない機種の本音を聞き出し、それを基に独自の予想を縦て情報を公開しています。
騎手が競走馬に当たる影響は無視できるものではありません。
騎手と競走馬の息が合えば実力以上の能力を引き出すことが多々あります。
Tendence
このプランでは血統や直前のレース成績など、いわゆるデータというものを一切利用せずに、担当馬券師の勘だけで買い目予想を出しています。
勘で予想を出す馬券師など不安しかありませんが、実績を見ればしっかりと結果を出していることは明らかです。
花の慶次郎
担当者である慶次郎氏は、競馬学会の出身でありながら、トラックマンに転向した異色の経歴の持ち主です。
トラックマンは競馬業界の関係者という事もあり、普通の人が知らないような密度の濃い情報を仕入れることができます。
VISION
競馬は時に人気先行のウマに馬券が集中し、思いもよらないオッズになることがあります。
VISONは、そういったレースを独自の方法で見抜き、買い目として情報を公開しているプランです。
Potential lab.
Potential lab.は、元生産育成研究室関係者が出している予想です。
馬のことを研究し尽くしているので、パドックなどを見て馬の調子がひと目で分かるのでしょう。
コルモゴロフ馬学
「万馬券の定理」という文字が目を引く予想で、その通り高配当の予想のみを公開しています。
実績を見ると、確かにどの馬券も150万円を軽く超えるものとなっており、的中すれば一攫千金が狙えます。
情報料はかなり高いですが、見返りも十分といえるでしょう。
KINGS MAN
競馬の本場であるイギリス生まれで、家族全員が競馬関係者といういわゆる競馬業界のサラブレットともいうべき人物が予想をしているプランがこの「KINGS MAN」です。
知識、人脈、行動力などすべてにおいて競馬学会の馬券師のなかでもトップレベルの能力を持っている馬券師なので、高い情報力に見合った利益をもたらしてくれるでしょう。
まとめ
競馬学会は新規ユーザーに対して「全額あんしん保障」という保険を提供しています。
これは90日間限定で有料情報を利用した際にその予想が当たらなかった、または情報料よりも配当金が下回っていた場合、ポイントで情報料を全額返還してくれるサービスとなっています。
返還されるのは現金ではない点と、馬券代が返還されない点には注意が必要ですが、それでもはじめて利用するユーザーにとってはありがたいサービスといえるでしょう。
有料情報は沢山の種類があり、担当者の予想の仕方もさまざまです。
担当者の予想の仕方に共感が持てるサービスを利用すると良いでしょう。
実際に馬券を購入して検証しましたが、的中率はとても高く、しっかりと利益を出せているので競馬学会は利用を検討してみてもよいサイトだといえます。